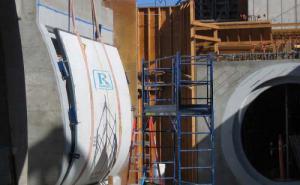
In any architectural and construction project, especially one built for public consumption, quality is paramount. It is simply not enough that the elements are carefully and professionally designed. The look, feel, and structural integrity of the actual work must be completed as advertised. The finished project will become just as much a reflection of the architect’s work – if not more – as it is of the individual tradesman putting the pieces together. Therefore, the pedigree of the structural and finishing materials used should be of great concern to the architect.
SPECIFYING MATERIALS
In many cases, perhaps all too often, general contractors are left to select which building materials are used. In the case of commonly accepted materials, this is often fine. However, keep in mind that even the most upstanding contractor is first and foremost a businessman. The architecture is then a product that must be produced within a budget and on time. No matter how important a specific project may be to the designer personally, the GC is not as likely to make the same distinction.
Architects certainly have the right to specify building materials and often do. The option to specify materials gives designers control over the virtue and finished appearance of their projects. In many cases, especially on high profile work, an architect will not leave the outcome of his or her project to chance. For example, the option to specify is increasingly being used on green projects, where the very intent of the architect’s vision would be lost without the right building materials. Material specification is also important in projects with load-bearing elements for both safety and aesthetic reasons.
Substandard materials can seriously degrade the appearance and perceived quality of a finished project. In this example, the low-grade acrylic panels that have been used on this pool edge are yellowing.
LIABILITY
Just as there is a professional risk in leaving material selection to another party, there can also be a liability in specifying if problems arise. Should the building components selected not perform to a satisfactory level, there is the possibility of being held liable for damages. What’s more, building components often will not fail until one or several years after the project’s completion. This can be the least opportune of times to discover that a specified material has defects, especially if it has been chosen for use in other projects in the interim. Therefore, take care when selecting materials to specify. Give due diligence in regards to the testing and quality practices of their manufacturers.
MATERIAL STANDARDS
Keeping up with the sheer amount of new materials that become available each year can be a daunting task, but one that is necessary in the industry. Each emerging trend in building components offers promising opportunities in design and customer satisfaction, but many products have not been appropriately tested and evaluated in the field. Standards for construction materials have many sources and are often broken down by industry. Thankfully, there are also resources that rate materials in a broad scope with ASTM being the international standards organization that is widely accepted. Take care to only recommend materials that are constructed and tested for quality within the guidelines of an accredited standards developing body.
REYNOLDS POLYMER QUALITY STANDARDS
In its nearly 30 years in business, Reynolds Polymer Technology has manufactured R-Cast® acrylic for over 1,600 projects. While R-Cast® has been featured in applications of nearly every shape and size, it has become best known for its use in large commercial aquariums. Numerous panels manufactured by Reynolds Polymer have set world records and were the largest such objects on earth at the time of their creation. R-Cast® is physically and chemically unique in the industry. It is made from a proprietary formula and cast in a single pour as opposed to laminating multiple, smaller sheets together. This gives the product an outstanding clarity and the ability to fuse panels with bonds that are nearly invisible, as monolithic acrylic does not contain the light attracting joints that laminated acrylic is known to possess. Reynolds Polymer Technology’s distinct product, dedication to quality, and corresponding success are hinged upon a stringent set of criteria that have been developed specifically for R-Cast® materials. While the acrylic’s applications have been numerous and varied, the specifications for finished products are not allowed to waiver.
SAFETY FACTOR
Acrylic panels can be subjected to pressure from thousands of gallons of water or hurricane-speed wind loads. Therefore, a safety factor that is many times beyond the minimum is necessary. All acrylic R-Cast® sheets are designed to a membrane tensile stress level of 800 psi. This design parameter gives a safety factor of 11.2 based on the ASME standard of 9000 psi tensile strength.
MATERIAL TESTING
Reynolds Polymer Technology places a great emphasis on the reliability and consistency of their products. R-Cast® acrylic is continuously tested according to ASTM standards in three separate areas: physical properties, optical validation, and optical performance as described below.
PHYSICAL PROPERTIES
Tensile Testing: This destructive test tells technicians about the strength and ductility of an acrylic sample. Tensile strength is used in determining the overall safety factor.
Compression Testing: The behavior of R-Cast® under crushing loads can be measured using this ASTM specified test.
Izod Notch Testing: By subjecting R-Cast® to the force of a pendulum strike, testers are able to determine its resistance to impact and overall toughness.
Shear Testing: A measure of the load at which acrylic will yield when sheared. Repeated tests and consistent results ensure a product that is safe and reliable under stress.
Rockwell Hardness: A determination of the permanent indentation left by a particular force. Consistent and even hardness results are obtained to determine how the acrylic will respond to likely sources of abrasion.
Flexural Testing: A measure of the force required to bend R-Cast® under four points of stress. This test simulates the deflection that the acrylic will undergo while under water pressure.
A Reynolds Polymer quality technician conducts a standard 4-point flexure test. The pressure being applied to the sample is carefully controlled by supporting and load pins.
OPTICAL VALIDATION
Haze: This test utilizes an objective haze meter in order to measure light-transmitting and wide-angle-light-scattering properties. Clarity, or the absence of haze, is an essential element in any R-Cast® viewing window that leaves the plant.
Dimensional Tolerances: Every acrylic panel by Reynolds Polymer, whether it be a standard or custom size, is subject to strict measurement tolerances. Length, width, thickness, and flatness are validated to ensure customer satisfaction.
Distortion via Grid Board: This evaluation is performed by viewing a finished sheet of acrylic in relation to parallel grid board with 1″ x 1″ squares. When illuminated, this configuration allows the tester to accurately check for broken lines, distortions, or inclusions.
A grid board of parallel squares allows for an objective validation of the acrylic’s viewing performance from the dry side.
OPTICAL PERFORMANCE
Spectrophotometer Testing: To precisely control the color of R-Cast®, a spectrophotometer is utilized to measure a panel’s reflection as a function of wavelength. The hue of the acrylic is kept within specific parameters so as to provide the best possible results for those observing from the dry side.
Liquid In-Process Validation: When the components of the proprietary formula for R-Cast® are being mixed, there are a number of variables that are indicative of a quality casting. Color, consistency and set-time are all analyzed at each stage of liquid manufacturing.
Validation of Raw Materials: Each and every element that is combined to make a Reynolds Polymer product must be evaluated for quality before being considered for use in casting. No component that fails to pass a raw material inspection is allowed to be introduced into the manufacturing process.
SUMMARY
There are portions of every job that will require specified materials. The reasons may be purely aesthetic, such as a particular type of roof shingle that accents the design’s flavor, or more technical, as in fireproof studs and framing materials. Some building components, such as R-Cast® acrylic, are designed to deliver both structural reliability and visual delight. When indicating the use of a particular construction or finishing material, it is necessary to consider not only one’s personal experience with the product, but also the methods by which the manufacturer controls quality and rates strength, hardness, and resistance to external forces. Reynolds Polymer Technology goes to great lengths in the testing of its acrylic according to ASTM guidelines. Quality is ensured by analyzing test results, exceeding industry standards, and following precedent taken from over 1,600 jobs involving the use of R-Cast® acrylic.
Are you interested in learning more about R-Cast® acrylic and how it may be the right material for your next project? Do not hesitate to contact a member of our sales or design team. Attachment C, a document with guidelines and specs for all R-Cast® products, is available for download.